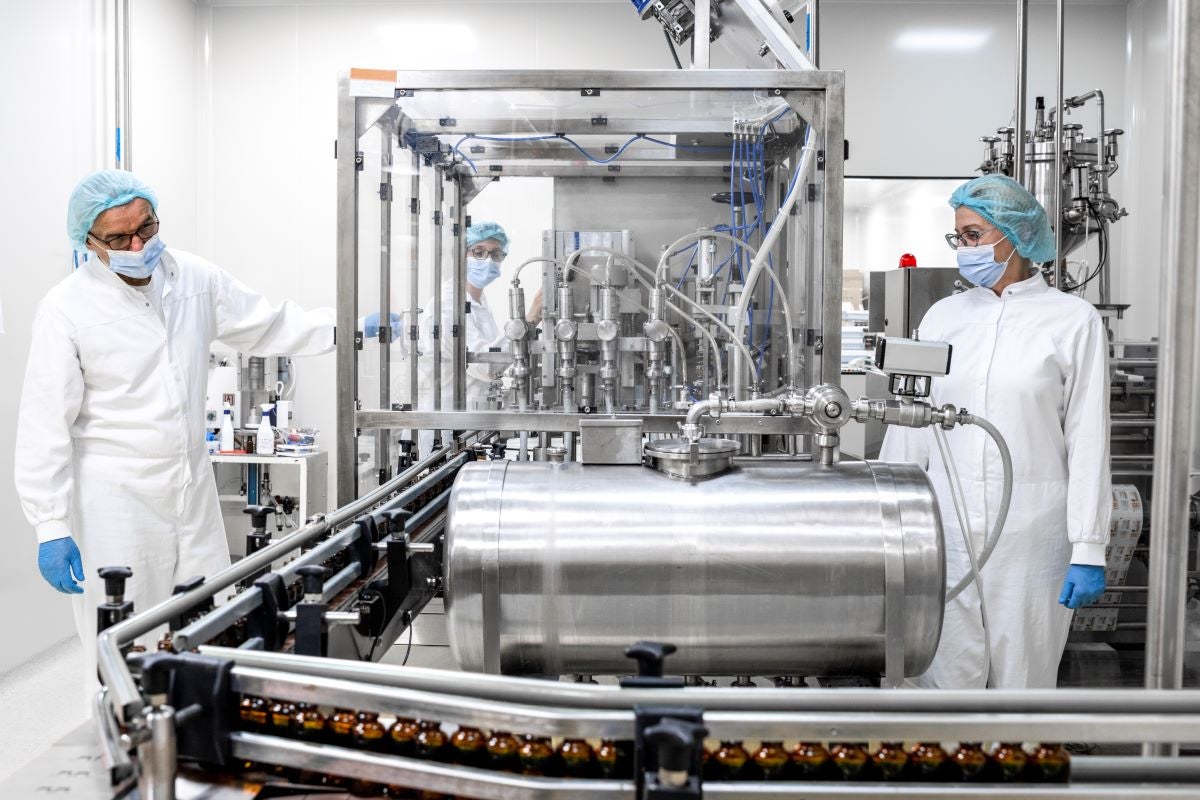
Trends in sustainability and quality assurance were key themes discussed amongst panelists at Convention on Pharmaceutical Ingredients (CPHI) Europe 2023, although the data reveals a lack of implementation of sustainable solutions.
In recent years, sustainability has become a trending term across various industries, including the biopharmaceutical sector. According to CPHI’s Annual Industry Report sustainability is a critical issue, “with 90% of executives citing ‘visibility on supply chain partner’s sustainability record’ as extremely important or important”.
Stakeholders across sectors have gathered at the ongoing 2023 United Nations Climate Change Conference (COP28) meeting to discuss initiatives to reduce carbon emissions and curb global warming to 1.5 degree Celsius below pre-industrial levels. At the recent pharmaceutical manufacturing-focused CPHI Europe 2023 conference, experts discussed how the biopharmaceutical sector, in particular, is taking a sometimes convoluted journey towards achieving sustainable practices.
Chief among the listed challenges was stringent regulations related to product safety and efficacy, as well as market pressures that have hindered the adoption of sustainable practices in the industry.
Still, experts noted that the application of sustainable practices and process efficiency are closely linked to each other, and that there is now a paradigm shift in the industry’s commitment towards more sustainable processes and greener formulations.
Access the most comprehensive Company Profiles on the market, powered by GlobalData. Save hours of research. Gain competitive edge.

Your download email will arrive shortly
We are confident about the unique quality of our Company Profiles. However, we want you to make the most beneficial decision for your business, so we offer a free sample that you can download by submitting the below form
By GlobalData
Don’t miss our coverage of COP28! Subscribe here for exclusive insights & analysis.
Green chemistry and continuous manufacturing can increase profitability
During a panel titled “Industry 4.0 – Setting the New Standard for Manufacturing Quality” experts discussed how eco-friendly practices not only have positive environmental benefits but can also increase an organisation’s profitability. According to Isamir Martinez, Scientific Alliances & Business Engagement Manager at ACS Green Chemistry Institute, applying green chemistry principles can help organisations maximise the efficiency of resources, leading to reduced solvent and reagent use, which in turn will translate into less energy consumption and waste. She also mentioned that artificial intelligence (AI) and machine learning (ML) are tools that can be utilised to create more streamlined and greener processes. Greener and more optimised processes can lead to the production of higher-quality products with less impurities and higher yields, which can increase a company’s profitability, she added.
Lawrence De Belder, continuous manufacturing practice lead at Pharmtech Associates, agreed that applying green chemistry solutions on the drug substance side can help excessive resource consumption. However, by implementing continuous manufacturing on the drug production side, organisations are able to produce the same amount of material on a smaller footprint, De Belder added. Specifically, there is less need for intermediate storage units/facilities with continuous manufacturing, leading to less overall electricity usage as all processes are connected to each other, as well as less water consumption for cleaning purposes.
Additionally, continuous manufacturing reduces excess material production, which would need to be incinerated, and thus it offers “a big improvement to the environment” in terms of carbon footprint, he added. De Belder thinks that in the future, each country’s government will impose improvement numbers to reduce carbon dioxide (CO2) emissions from companies over time. Therefore, “companies will need to find solutions for this, and continuous manufacturing will be one of the potential ways to do it”, he stated.
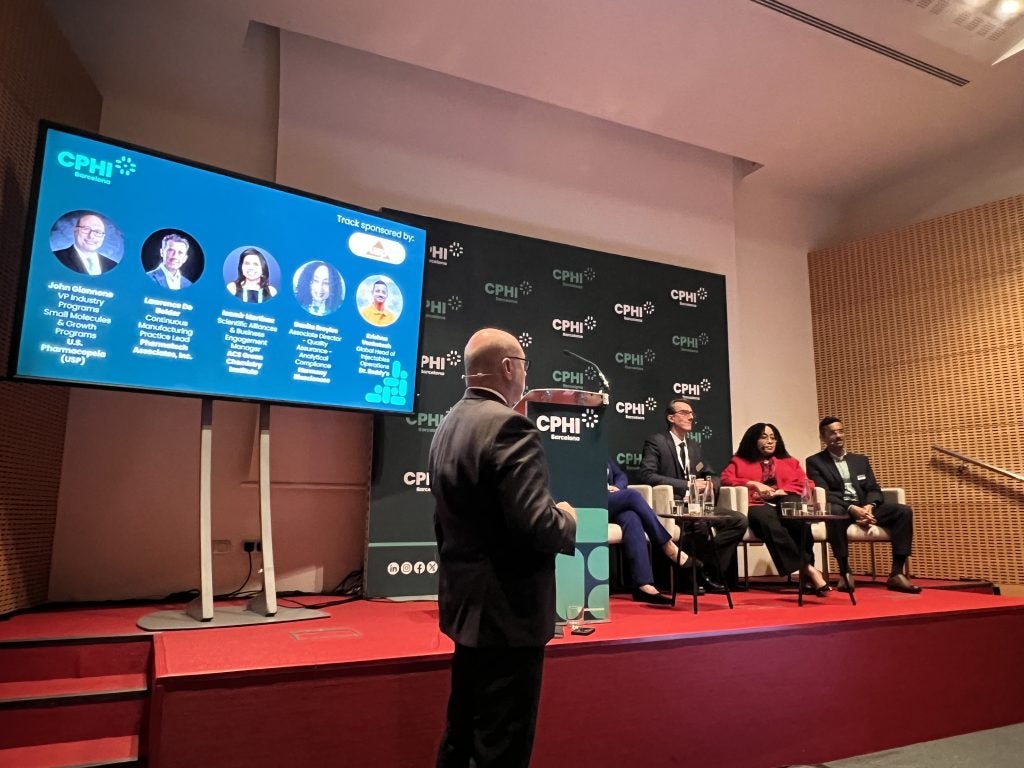
Krishna Venkatesh, global head of Injectables Operations at Dr Reddy’s Laboratories, highlighted that digitisation is necessary for continuous manufacturing in the future. Venkatesh emphasised that Dr Reddy’s Laboratories is preparing to enter a “zero touch” era where the goal is to reduce variability in the manufacturing process by minimizing human involvement and enhancing digital capabilities. The approach involves digitising operational systems (utilising electronic batch records), deploying sensors and data acquisition systems, and utilising AI engines for data analytics to create “a correlation between quality attributes and process parameters”. The emphasis is on transforming data into actionable insights to improve processes and facilitate more intelligent decision-making in manufacturing, which will “enable continuous manufacturing in a very powerful manner”, he added.
Danita Broyles, associate director, Quality Assurance-Analytical Compliance, Harmony Biosciences, San Gabriel, California, US agreed that transition from paper-based to digitized systems is crucial and emphasised its ability to seamlessly connect data across manufacturing steps. This interconnected digital approach enables efficient problem-solving, allowing for the identification of issues such as compression problems and discerning whether they stem from equipment or ingredients, she added. The focus is on utilising digital systems to streamline processes and enhance efficiency, even in smaller pharmaceutical companies where manpower may be limited, Broyles stated.
Disparity between industry sentiment and actions
While sustainability was an underlying theme discussed across multiple panels and presentations in this year’s CPHI Europe conference, a consensus on achieving it was lacking. According to a report by Doug Nissinoff, Senior Research and Strategy Associate at BioPlan Associates Inc, which was included in CPHI’s Annual Industry Report, while the “industry shows a notable inclination toward eco-friendly and sustainable solutions, the existing infrastructure and operations contradict these aspirations”.
Data included in CPHI’s Annual Industry Report reveals a “concerning reliance on less sustainable methods: for instance, a staggering 40.7% of facilities resort to incineration as medical waste, despite only 18.5% of respondents seeing this as an ideal practice”. Additional data reveals that even though there is an “overwhelming sentiment favoring the recycling of single-use devices by sending them back to manufacturers; nearly half of the respondents (48.1%) believe this should be the norm, yet a meager 4.9% of facilities implement such practices,” according to the report. Such divergence between the industry’s expressed notions and actual implementation of sustainable solutions highlights a need for further action.
A true transformation towards sustainability requires a mindset and organisational change, as well as for revenues and economic incentives to be dependent on sustainable initiatives, based on CPHI’s report. According to Nissinoff, “while awareness of sustainable disposal methods is present, systemic changes and infrastructure investments are imperative to bridge the existing chasm and align actual practices with the collective vision for a greener biopharmaceutical future.”
Stricter supplier assessment is critical
On the topic of ingredient quality, all experts expressed a deep concern for the potential product safety and efficacy risks associated with diversity among suppliers and their significant impact on patients’ lives. During the panel discussion, Broyles challenged the notion that all suppliers/vendors are equal in terms of substance quality, emphasising the need for robust supplier qualification programs across different vendors and even across one vendor supplying different multiple substances. Broyles stressed the importance of thorough qualification beyond a checkbox process, with a call for critical conversations within companies to establish the necessity of scrutinising suppliers even within the same window of materials. Additionally, the panel speakers considered the complexities in the excipients industry, where variations in raw material sources can impact product quality, which is more relevant than ever due to sociopolitical challenges in certain regions.
The panelists focused on the need for a nuanced approach to supplier qualification, considering specific company and product requirements and potential variations in the supply chain. More specifically, Broyles emphasised the importance of addressing problems upstream in the supply chain through measures like strict vendor assessment, routine audits, and asking the right questions to ensure the quality of ingredients. She cautioned against overly attractive deals, stating that “if something seems too good to be true, it probably is”. She also stressed that the responsibility lies with pharmaceutical companies to secure their supply chains, remove rogue suppliers, maintain stringent supplier qualification processes, and follow regulations and guidelines meticulously, citing instances where failure to do so has resulted in FDA warning letters.
However, high quality product standards dictated by regulatory bodies may hinder sustainability efforts in some cases. According to CPHI’s annual industry report, “the FDA and EMA have set the standard for product quality and this makes sustainability initiatives difficult to implement”. In some instances, there is a critical question of whether a company is willing to risk sacrificing product efficacy by switching reagents to achieve greener formulations. While sustainability initiatives can limit resource consumption and increase profitability, “demonstrating a return on investment (ROI)” and “convincing boards to invest in sustainability initiatives” make this challenging, according to the CPHI report.
Sign up for our daily news round-up!
Give your business an edge with our leading industry insights.