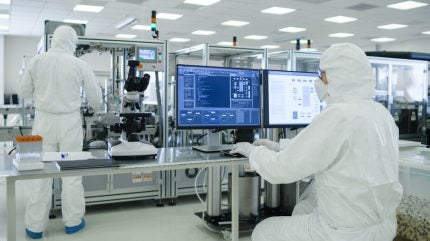
Competitive pressures and technological advancements compel pharmaceutical companies to launch new products rapidly. Outsourcing to contractors can help accelerate this process, but it is crucial to conduct due diligence to ensure that regulatory requirements and best practices are adhered to, especially when dealing with highly potent active pharmaceutical ingredients (HPAPIs).
The role of CDMOs in the pharma supply chain
Contract development and manufacturing organisations (CDMOs) play a crucial role in the drug product supply chain by offering development and manufacturing services for their clients’ pharmaceutical products. According to GlobalData, there are around 500 CDMOs globally, with more than 30% involved in the development and manufacturing of drug products containing highly potent APIs. Considering the potential hazards of these types of substances, safety and containment, product integrity, and regulatory compliance are paramount.
Regulations for HPAPIs around the world
If drug products containing HPAPIs are to reach their intended markets, their development and manufacturing processes must comply with both national and international regulatory frameworks by following good manufacturing practices (GMPs), occupational safety and health standards (OSHS), and waste disposal legislation to ensure patient and personnel safety, facilities, and containment.
Regulations regarding the sterile processing of highly potent products impose stricter handling and safety requirements than those for non-sterile drug processing. Frameworks such as Occupational Health and Safety Management System (OHSMS) 18001 and ISO 14001 establish clear safety and environmental standards for HPAPI processing. US and European cGMP guidelines cover cross-contamination, equipment cleaning, and material handling, while FDA guidance on aseptic processing includes ingredient containment during manufacture. These are overlayed with key International Organization for Standardization (ISO) standards, including ISO 13408 (aseptic processing), ISO 14664-1 (cleanrooms), and ISO 11134, 11137, and 14937 (sterilisation).
Although regulations and standards covering HPAPIs have similar themes and focus on containment, cleaning, and handling, the sheer volume of requirements and differences among them can be extremely challenging. Therefore, constant monitoring of compliance and evolving best practice methods must be a key task to meet the requirements of changing regulations to minimise legal and operational risks.
HPAPIs and occupational exposure limits
The starting point for assessing the requirements for a drug product containing HPAPI is determining the potency of the active ingredient. In pharmaceuticals, an active pharmaceutical ingredient (API) is a substance with pharmacological activity in a finished drug product and is classified as an HPAPI if it exhibits biological activity at doses below 150μg/kg of body weight, binds to specific receptors, is oncogenic, or causes developmental defects. HPAPIs with an occupational exposure limit (OEL) below 10μg/m³ (eight-hour average) are often considered highly potent, requiring specialised handling and containment. These are divided into occupational exposure bands (OEBs) – essentially, the higher the OEB number, the greater the exposure and the higher level of containment required.
However, there is no universal definition regarding occupational exposure banding, and these can differ from company to company and from regulator to regulator. Additional challenges when manufacturing with HPAPIs includes varying containment and handling regulations, which differ across agencies and markets, adding further complexity to compliance and operational processes.
“There is a lack of consistency regarding the assignment of occupational exposure limits (OELs) to specific bands, and a significant lack of common terminology and, therefore, a true understanding of potent classification,” says David O’Connell, Director of Scientific Affairs at PCI Pharma Services, a CDMO which provides sterile and high-potent drug development and manufacturing, clinical trial supply, and commercial packaging services.
O’Connell advises that when developing and manufacturing highly potent drug products, there should be an OEL monitoring programme at each stage of the process. These monitoring programmes should include strict cross-contamination controls and risk assessments of potential contamination from air, equipment, personnel, and contact surfaces.
Using the most suitable banding system for the specific HPAPI is critical for containment during the development and manufacturing process. The banding system is especially important for early-phase development compounds, where potency is estimated rather than measured due to limited toxicology data. These estimates help ensure safe handling during initial project phases. Nevertheless, as the substance transitions from preclinical to clinical development, accurately determining the API’s potency becomes essential to meet regulatory requirements and ensure proper management throughout drug development and manufacturing.
Containment solutions for HPAPIs
While safety technology testing guidelines exist, there is limited regulatory guidance on facility design for CDMOs that handle HPAPIs.
As Kate Smith, Director of Quality at PCI points out: “From a facility build and design point of view, there’s not one design or regulation where it says “this is what you need” in terms of blueprints for a contained high-potent facility. The design will depend on a multitude of factors including equipment selection and cleanability, utilities selection, the targeted products and the operational controls. At the design stage of the facility build here in Tredegar, PCI took the proactive approach of reviewing and assessing all guidance from FDA, UK, EMA, ANVISA, PIC/S and ISPE pharma baseline guides. We then collated all the best practice of the industry to ensure that we were designing to meet the global regulatory landscape.”
The International Society of Pharmaceutical Engineering (ISPE) offers pharmaceutical knowledge and advice on key issues facing the pharmaceutical industry. These include manufacturing and supply chain management, operational challenges, and regulatory insights to aid facility design, clean room standards (ISO 14644), handling, and contamination control.
However, the potency of an HPAPI is a key element when assessing production, processing, and capacity and applying the optimal containment technology in a CDMO. “At PCI, we use that information to determine where and how to process materials in terms of the level of containment needed,” adds O’Connell. “We look at the capabilities at our facility to determine if the systems we have in place are sufficient to ensure we can handle the specific material in a safe, compliant, and contained manner. If necessary, we then work with our in-house engineering team to fine-tune our systems to the project.”
In addition, maintaining good relationships with technology suppliers is vital due to limited facility design guidelines mentioned previously. As a result, operations involving HPAPIs are often customised. Containment technology developers are at the forefront of advances in HPAPI technology and are better positioned to identify improvements and access advanced solutions to containment and handling requirements. Developers are fully aware of how bespoke containment systems should align with ISPE testing guidelines, ensuring compliance and optimised performance for handling highly potent drug substances.
Preventing cross-contamination in high potent manufacturing
Avoiding cross-contamination in facilities where HPAPIs are handled is critical to ensuring product safety, regulatory compliance, and worker protection. As Smith notes: “To ensure containment, there are other CDMO facilities that use only PPE to protect the operators and they don’t look at facility design like we do, which isn’t wrong, as long as they’ve got the right controls and strategy – it’s very difficult to do a one shape fits all.”
Key areas that can help mitigate risks include facility design, containment technologies, cleaning and validation, personal protection equipment, and extensive staff training, as well as monitoring and testing.
When designing a facility that handles HPAPIs, one of the main considerations is the need for segregated production spaces – or entirely separated and dedicated facilities – for HPAPI handling with directional airflow control and high-efficiency particulate air (HEPA) filtration systems to contain airborne particles. On top of this, establishing clear containment zones and restricting access to high-risk areas reduces the probability of cross-contamination.
Within high potent CDMOs, technologies used for containment comprise closed systems that use isolators, gloveboxes, or other closed systems, combined with single-use technologies, such as disposable equipment that helps reduce cleaning requirements and contamination and minimises exposure.
Robust cleaning and validation procedures are also a vital consideration, involving the establishment of protocols and audits to ensure compliance and create standardised routines for maintaining a sterile environment. To verify the cleanliness of facilities, swab and rinse sampling should also be conducted on a regular basis. Regular audits of cleaning validation and equipment reviews are also undertaken to ensure ongoing compliance.
Employer protection is crucial due to the hazardous nature of handling many HPAPIs within a multi-product facility, and requires personal protective equipment (PPE), including powered air-purifying respirators (PAPR), gloves, and suits. In parallel, staff training and knowledge of the types of HPAPIs being handled is equally as important so that they are aware of contamination risks, handling procedures, and emergency protocols if an incident occurs.
All the above should be backed up by quality assurance and documentation, including guidelines of standard operating procedures (SOPs) for containment processes. There must also be regular audits covering environment, health, and safety reporting. This is alongside inspections by internal teams and regulatory bodies and clear documentation, maintenance of batch records, validation reports, as well as monitoring data.
Conclusion for CDMOs on facilities management
In the specialist field of high potent development and manufacture, safety, compliance, and efficiency are of utmost importance. Effective containment and handling strategies are crucial for minimising risks to personnel, products, and the environment. Every aspect must be stringently managed, from facility design and cleaning validation to staff training and advanced containment technologies.
To read more about the role of PCI in the delivery of life-changing therapies, download the white paper here.